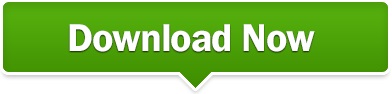

- Digital techniques for power system protection usask driver#
- Digital techniques for power system protection usask full#
- Digital techniques for power system protection usask Pc#
Half step drive, where the current in the coil is turned off for one step period before being turned on in the opposite direction, has been used to double the step resolution of a motor.
Digital techniques for power system protection usask full#
The complete full step sequence is shown in figure 2. To step the motor, the current in one of the two coils is reversed and the rotor will rotate 90 degrees. In classical full step operation an equal current is delivered to each of the coils and the rotor will align itself with the resulting magnetic vector along one of the 45 degree axis. The simplified model of a stepper motor is a permanent magnet rotor and two coils on the stator separated by 90 degrees, as shown in Figure 1. In either case the basic theory of operation is the same. Microstepping a stepper motor may be used to achieve one or both of two objectives 1) increase the position resolution or 2) achieve smoother operation of the motor. Examples show the implementation of microstepping drives with several currently available chips and chip sets. This application note willĭiscuss implementation of microstepping drives using peak detecting current control where the sense resistor is connected between the bottom of the bridge and ground. Many designers today are seeking alternatives to increase the resolution of the stepper motor drives. However their resolution, when driven in the conventional full or half step modes of operation, is limited by the configuration of the motor. Stepper motors are very well suited for positioning applications since they can achieve very good positional accuracy without complicated feedback loops associated with servo systems.
Digital techniques for power system protection usask driver#
Microstepping Stepper Motor Driver Circuit

In addition several key functions such as protection circuit and PWM current control drastically reduce external components count to meet requirements for many different applications. The principal aim of this development project was to produce an easy to use, fully protected power IC. These features, including a decoding logic that can generate three different stepping sequences, allow the device to be used in many applications including microstepping. This IC is a one-chip cost effective solution that includes several unique circuit design features. The L6208 is a fully integrated stepper motor driver IC specifically developed to drive a wide range
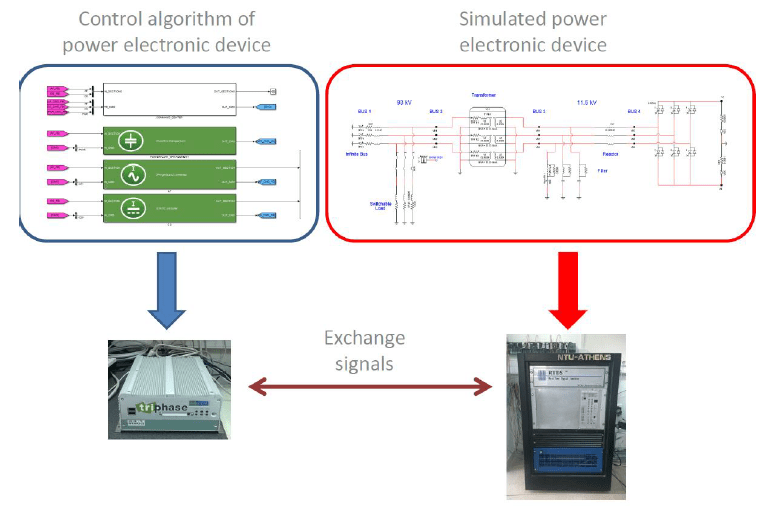
Modern motion control applications need more flexibility that can be addressed only with specialized IC products. L6208 FULLY INTEGRATED TWO PHASE STEPPER MOTOR DRIVER This function is particularly useful when the spin speed is very low, in the order of fractions of rpm. As an example, a 200 steps motor could behave like "a virtual" 12.800 steps motor. The more interesting aspect of this circuit is its ability to implement the microstep technique and to multiply up to 64 times the motor real steps number.
Digital techniques for power system protection usask Pc#
Moreover the digital interface allows to connect up to six motors to a single PC parallel port. The circuit is, for safety reasons, optically isolated from the PC and it allows to manage motors up to 3A for phase. This circuit allows to connect a bipolar step motor to a personal computer through the parallel port. Up to 9 PIC in/out pins can be allocated to The PIC has plenty of left over rom if you need to do motionĬontrol or use the board as the complete brains and driver forĪn entire machine. Is 3600 steps/rev, almost stepless operation. Have provided also will do pwm and give 18th stepping, which The brain has control of which of the 4 transistors are ON,Īnd sets 3 possible current levels, enough to do 6th steppingĪnd give 1200 steps/rev with hardware alone. Large currents, but it's simple and accurate enough with the This causes a "set" voltage across the sense resistor Rs, ie Setting the base of the main transistors at a "set" level, then The constant current system is crude but simple, it relies on The motor must haveĥ or 6 wires (or 8), as 4-wire motors are only for bipolarĪnd 4-WIRE MOTORS WILL NOT WORK WITH THIS BOARD. It is a unipolar (or 5-wire type) driver. First, it allows a stepping motor to stop and hold a position between the full or half-step positions, second, it largely eliminates the jerky character of low speed stepping motor operation and the noise at intermediate speeds, and third, it reduces problems with resonance.Īlthough some microstepping controllers offer hundreds of intermediate positions between steps, it is worth noting that microstepping does not generally offer great precision, both because of linearity problems and because of the effects of static friction.
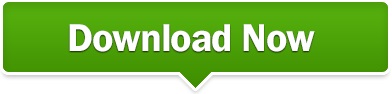